Our Work
Below are a few projects PDC has worked on to give a preview of how PDC can help your manufacturing process. Enjoy the read and imagine how PDC can help you.
PDC transformed a laser welding process from non-capable, non-controllable process to highly capable and controllable process in a matter of weeks.
Scrap was reduced to zero! Production was able to increase the number of units per hour produced!
Check out the stats below, the process went from a Ppk of -0.37 (Before) to a Ppk of 3.10 (After).
This is greater than 6 sigma capable!
Less than 1 defect in 3.4 MILLION parts will be produced!
Use the slider below to check out the improvement!
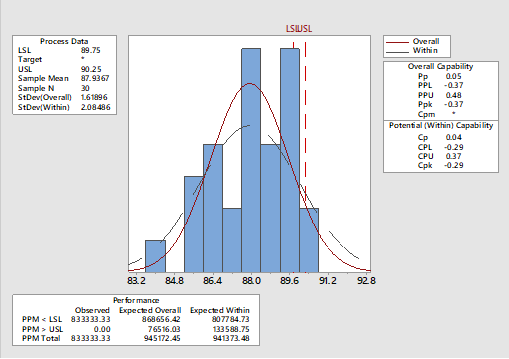
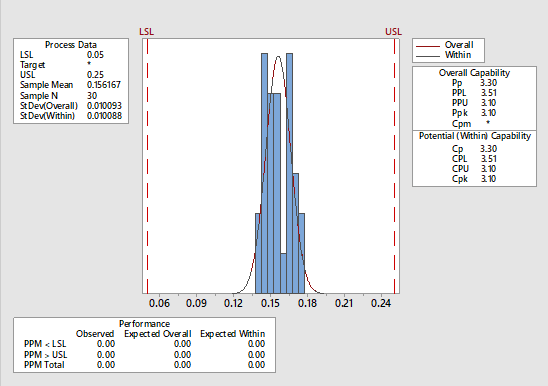
Don't know what equipment to purchase?
Don't know if the equipment you have is suited to the task?
Don't know where to start?
Well don't worry. PDC has extensive experience at determining what equipment is best suited to a particular task, so you don't have to.
A customer of PDC was using the same machine for years but couldn't determine why the machine wasn't suitable, just that it caused failures and scrap.
PDC performed an equipment analysis below that not only showed why the current equipment wasn't suitable, and could not be modified to suit the task. However, PDC discovered an alternative solution that meets the requirements of the task much better.
A new machine was purchased, qualified and the process developed to an exceptionally high standard, all through PDC.
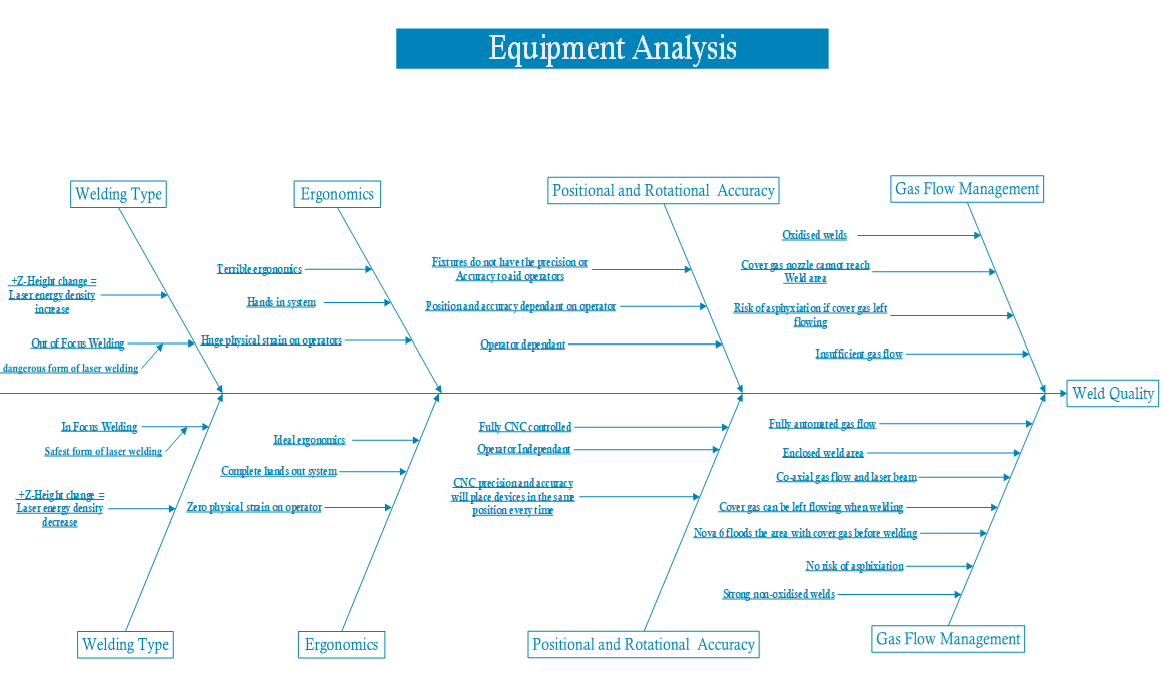
PDC has worked on multiple rapid improvement projects with customers. This work typically involves looking at a manufacturing method or product design and developing out of the box ideas to increase UPH (units per hour), i.e. making products faster and more efficiently.
Some projects only take a week or two until new fixturing is ready to be installed. Take for example the below bar chart. PDC was able to increase the speed of loading stents into catheters by a factor of 7 without any major equipment changes!!!
This involved using "Compliant Fixturing" to reduces stresses on the stent itself. This project was completed in less than 2 weeks with clear UPH benefits.
As PDC treats the confidentiality of our customers extremely seriously, PDC cannot display the Solidworks model or an image of the "Compliant Fixturing".
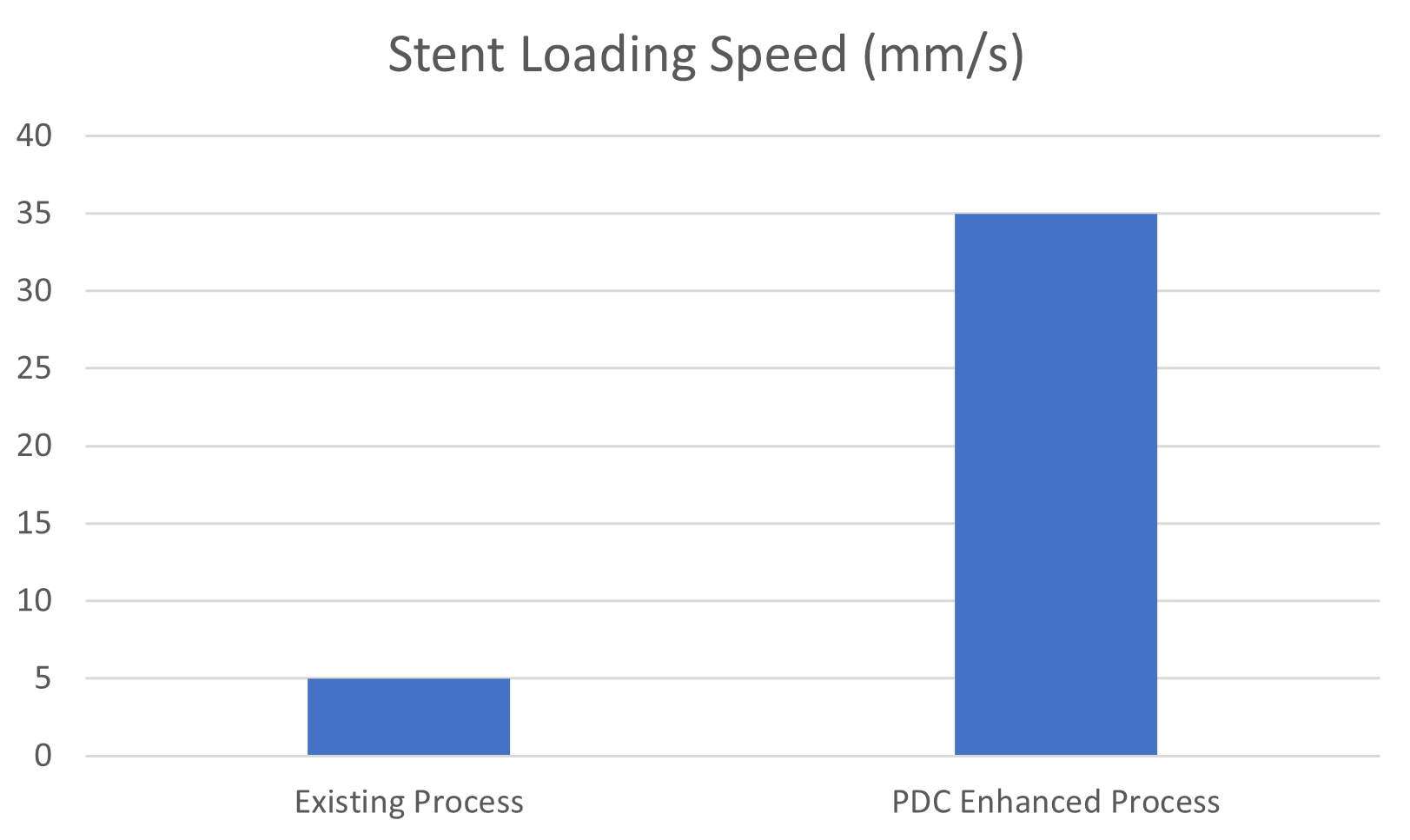
PDC also offers an engineering consultancy services and often works with R&D & PD teams to ensure that the product they are designing are manufacturable, cost effective and time effective.
PDC can create prototypes and test solutions for customers and demonstrate concepts that meet our customers expectations.
Our 3D printing services can rapidly print concepts ready for initial concept testing. Concepts that prove promising will be sent for machining and additional testing.
Often PDC is faced with a product that must meet several design criteria at once, be it, weld depth, hermeticity, strength, loading forces etc. etc. If full prototypes were to be manufactured for every test, costs would spiral out of control.
PDC will breakdown each design criteria and design specific prototypes to test each design criteria individually (known as first principles testing). This approach reduces cost and leadtimes and allows customers to test the concept in bite size chunks rather than one massive test case involving significant cash investment.
A customer recently contacted PDC to develop a first principles approach for a project where hermeticity was a major concern. The customer initially attempted to get prototypes for testing and received a quote in excess of €36,000.
PDC was able to design a first principles test method and demonstrate how the test prototypes would function. The results were exceptional:
-leadtimes were reduced from months to weeks
-Samples numbers were tripled to gather as much data as possible
-Cost was reduced to €24,000 for 3X number of samples
This was an exceptional result and PDC saved the customer €12,000 in a matter of days!
Don't delay, ease the stress today!
Contact PDC straight away.